How To Restore Parquet Flooring?
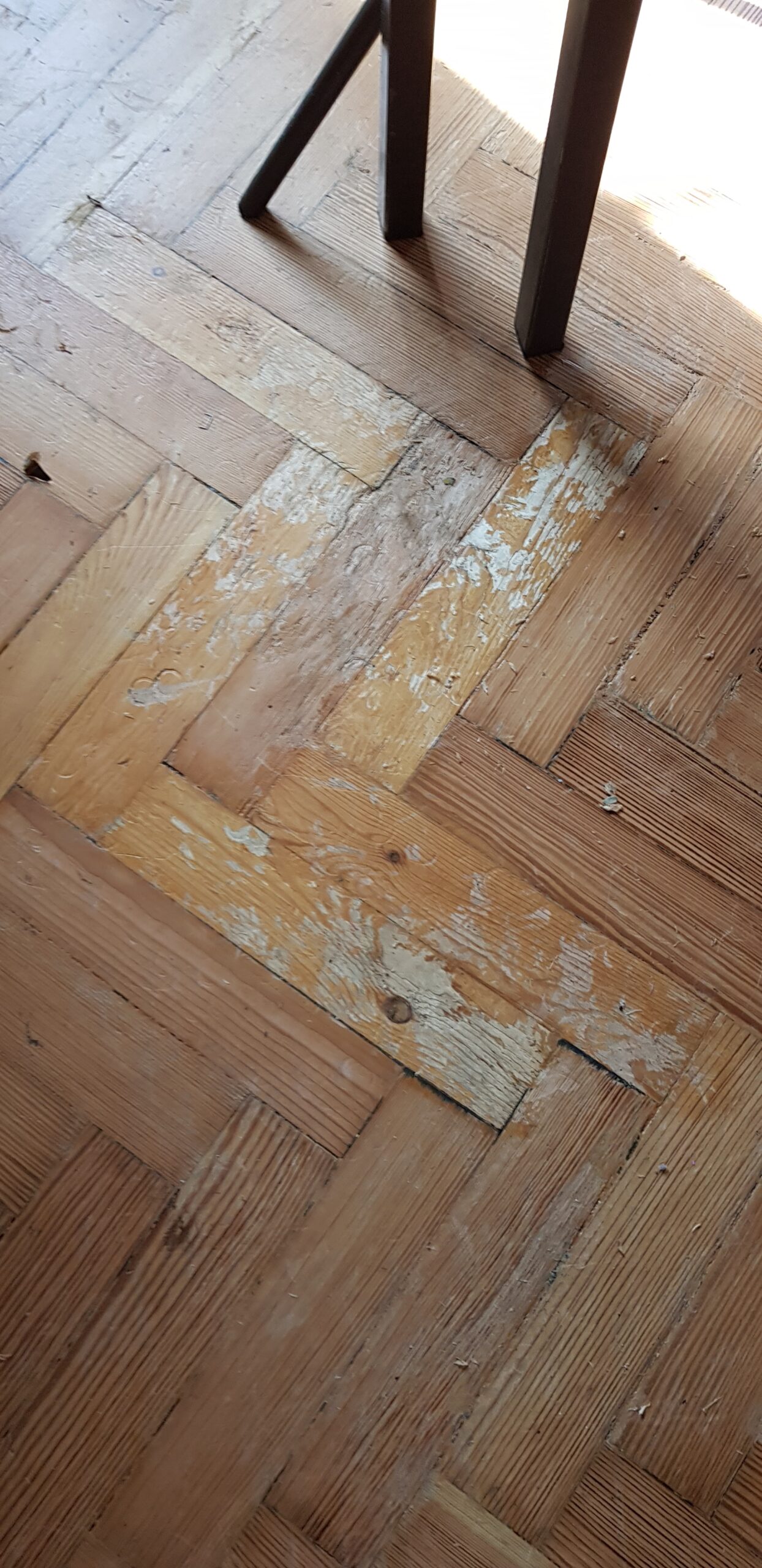
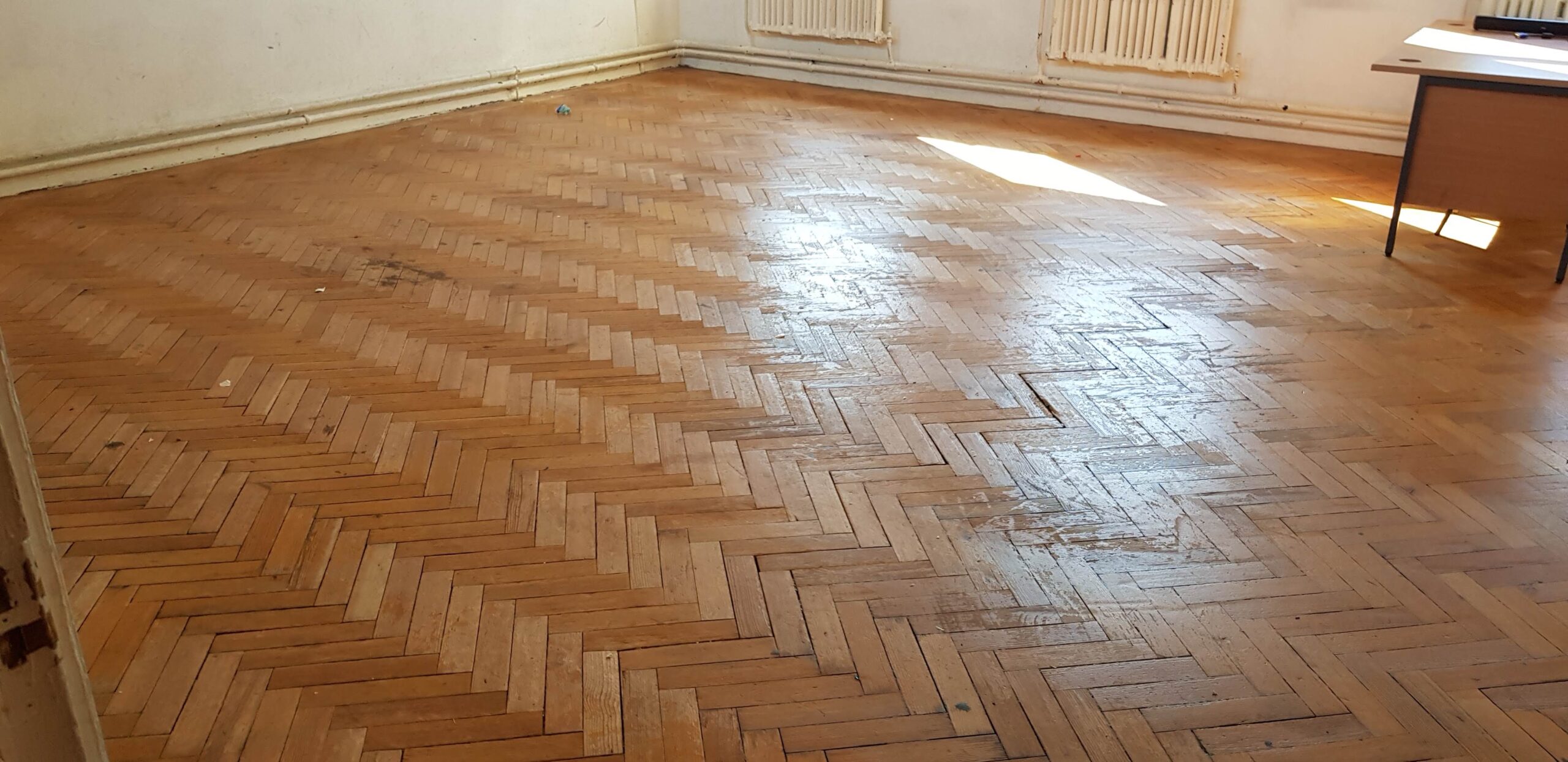
The Parquet Flooring Restoration Process
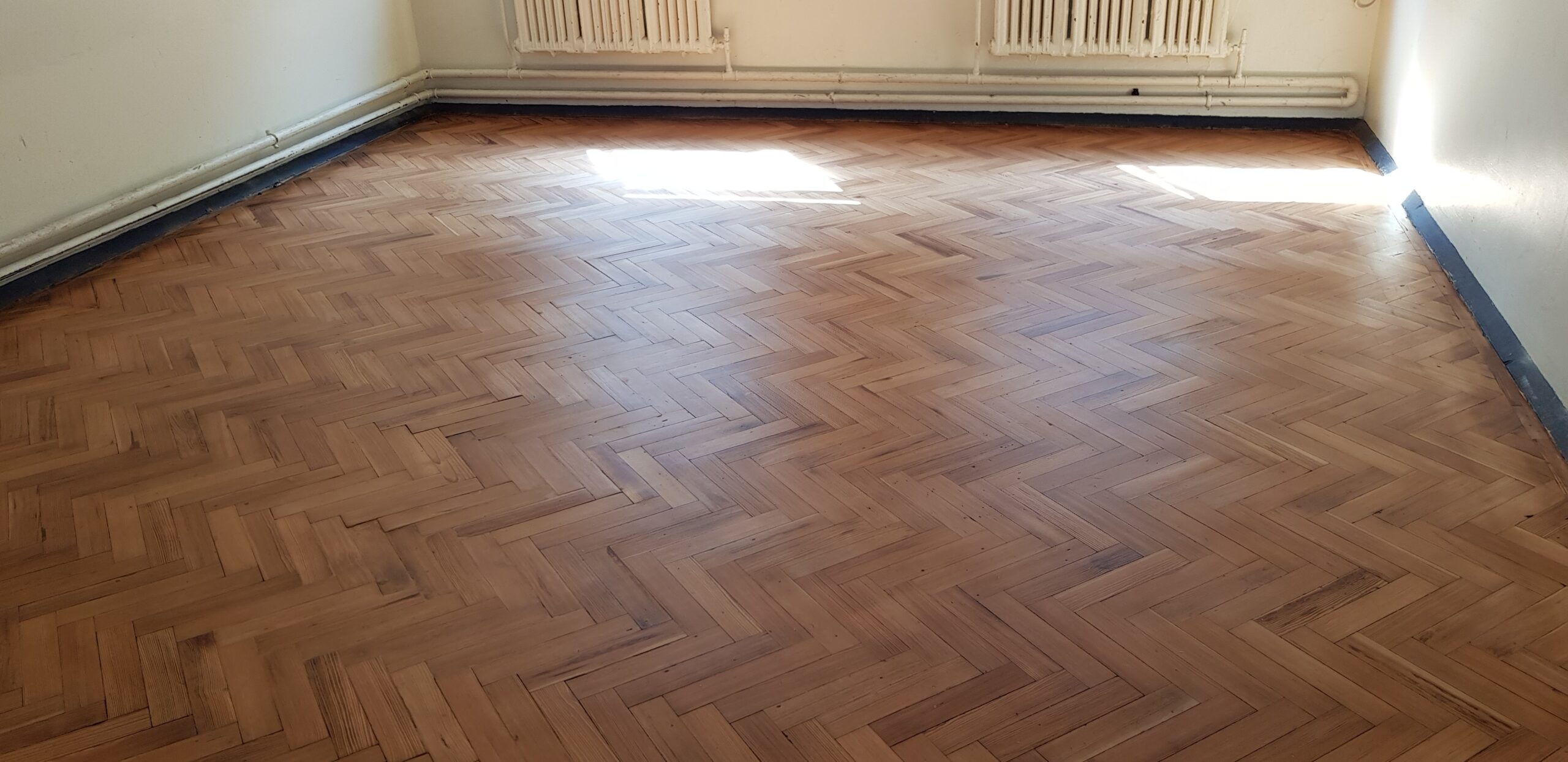
Once the stain had dried, we commenced with the polishing. French Polishing is a very delicate process, requiring multiple applications to achieve the desired finish. In the end, we applied 9 coats of shellac polish to reach the clients satisfaction! Each coat of polish is very thin and builds upon previous coats to add depth and richness to the staircase. Although, for us, most important of all, is that French Polish will start to dry almost immediately! Each coat must be precisely applied for maximum effect, as there’s no room for error. Should your hand start to stray, you don’t have time to touch it up after or you risk tearing the finish. Long, continuous strokes are needed to apply the polish correctly, as it dries so fast that a careful eye can tell in which direction (and even how) the polish was applied.
In total, we coated up 20 steps, door thresholds and several handrails throughout the house, but you have to remember that each was carefully coated 9 separate times! 180 individual applications of French Polish, but we think you’ll agree that the end result was well worth it.
French polishing gives a superb finish and is extremely adaptable. It gives the highest quality finish that improves in time like a vintage wine. As well to fine homes, we have also been commissioned on private jets, luxury boats, banks, embassies and hotels.